How does cold spraying work?

Cold spraying is a cutting-edge technique in the realm of thermal spraying

In comparison to conventional methods, cold gas spraying presents distinct advantages. Unlike traditional processes, the spraying material undergoes neither fusion nor melting during the procedure. This characteristic opens the door to a more extensive and adaptable array of applications when contrasted with other thermal techniques.
The particles' elevated kinetic energy and the pronounced degree of deformation upon impact with the substrate facilitate the creation of uniform and exceptionally compact coatings. The scope of coating thickness spans from mere fractions of a millimeter to several centimeters.
Primarily, metallic coatings are generated using this method, possessing physical and chemical properties that closely resemble those of the base material.
Utilizing the state-of-the-art system technology developed by Impact Innovations GmbH, a process gas—primarily nitrogen or helium—is introduced into a spray gun under pressures of up to 50 bar (725 psi). This gas is then heated within the gun housing to reach a maximum temperature of 1100°C (2012°F).
Subsequently, the heated and highly pressurized gas expands through a convergent-divergent nozzle, transitioning to ambient pressure.
This expansion drives the process gas to achieve supersonic velocities and, simultaneously, cools it down to temperatures below 100°C (373°F).
Within the convergent section of the nozzle, spray powders are introduced using a powder feeding unit and carrier gas, propelling them to particle speeds of up to 1200 m/s within the primary gas stream.
Upon impact with the component's surface, the highly focused spray jet causes the particles to deform and adhere, creating a robust and cohesive coating with minimal oxidation.
This process is particularly effective even on untreated surfaces.
Learn more about cold spray in this video:

Cold spraying particle velocity as a measure of layer quality and efficiency
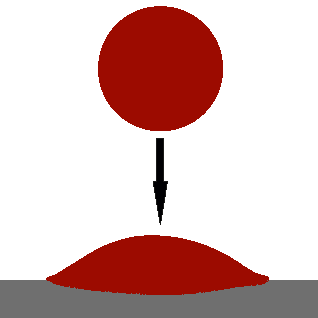
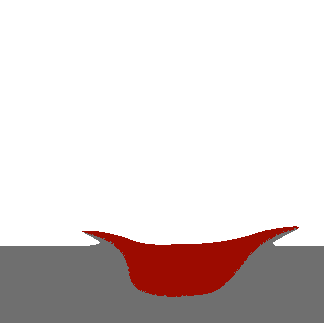
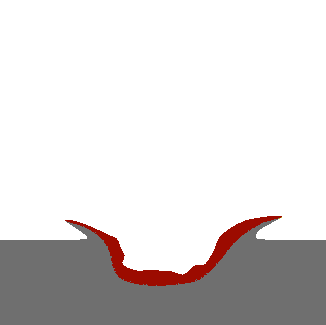
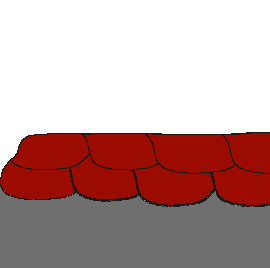
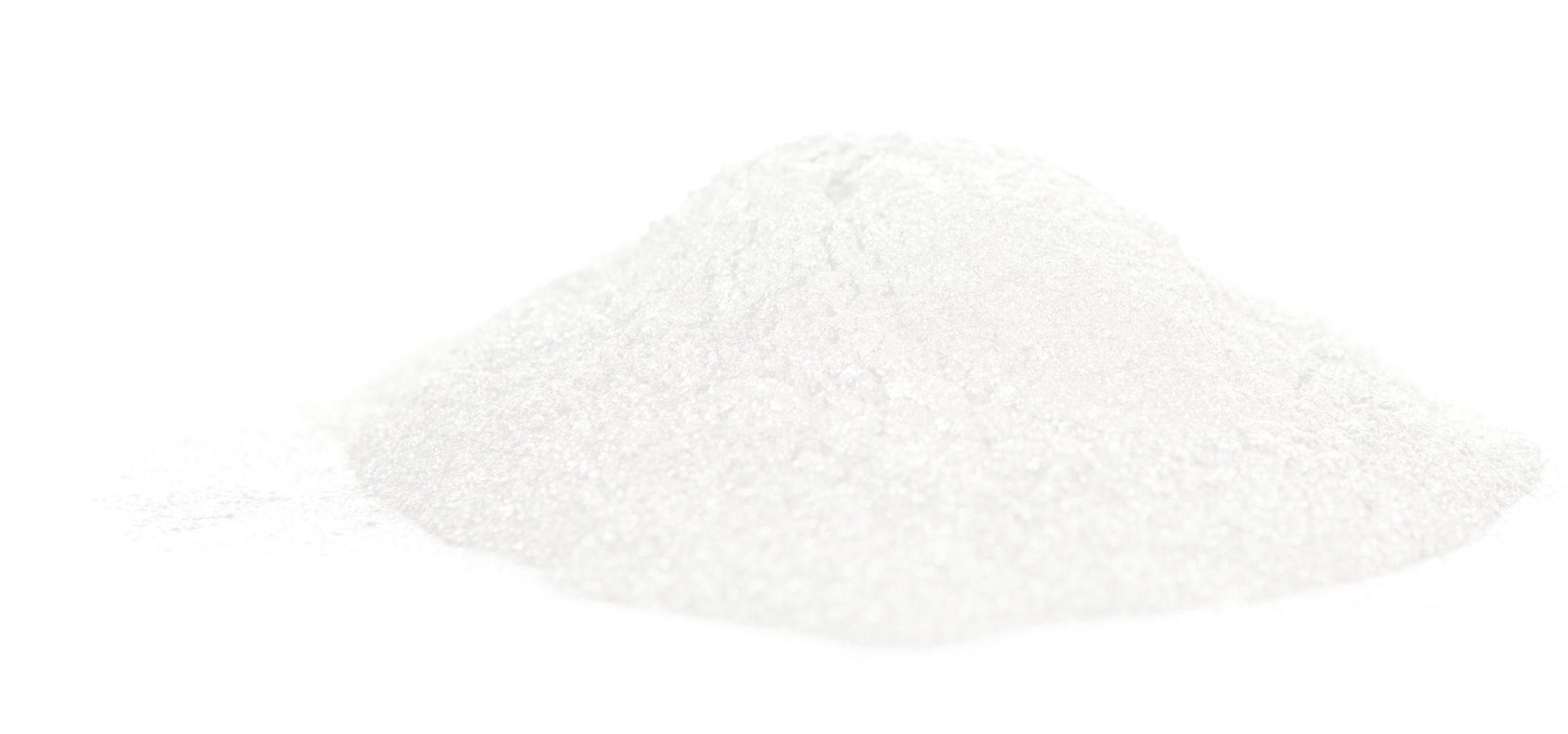
What can be coated by cold spraying?
Individualized Processing